Introduction to Diesel Engine Development
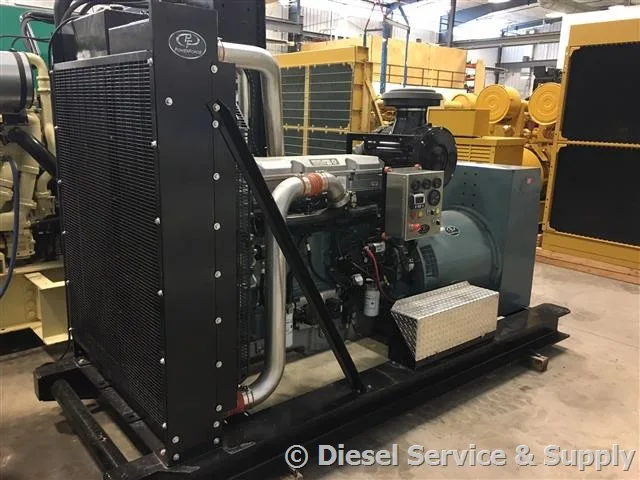
The diesel engine was developed over a century ago and was instrumental in replacing the steam engine. After the death of its inventor, Rudolf Diesel, the diesel engine underwent a lot of changes. Even today it has a great potential for modifications to make it more efficient with respect to fuel economy, power output, and cleaner exhaust fumes. Although gasoline engines have surpassed the diesel engine in popularity, recent advances in diesel engine technology and fuel systems will likely make the diesel engine the most desirable for heavy transport, agriculture, backup power, and other systems for the years to come. Cummins, Caterpillar, and other leading diesel engine research and manufacturing companies are constantly breaking new ground to develop innovative digital technology and treatments to refine the traditional diesel engine.
Diesel Engine Efficiency and Modification
Combustion Process and Efficiency
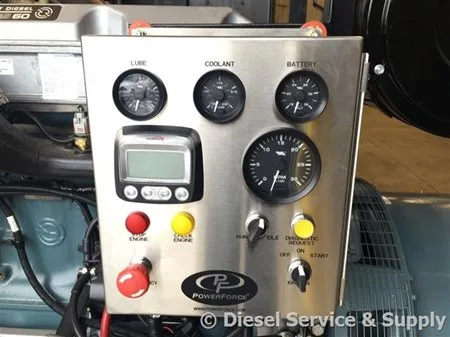
All engines produce power by igniting a mixture of air and fuel to produce energy. In gasoline engines, a spark plug is used to perform the initial ignition. However, in diesel engines, this ignition is performed directly, without the use of a spark plug. Initially, air is introduced into a combustion chamber. The air is then highly compressed. This process of super compression heats the air to as high as 1000 °F. Fuel is then directly injected into the combustion chamber through a pre-chamber. The extreme heat causes the fuel to vaporize and ignite. As the air is further heated by ignition, it expands, driving the pistons that work the crankshaft. The efficiency of a diesel engine depends on how efficiently the droplets of fuel are injected into the pre-chamber. The smaller and more widely distributed these droplets are, the better the efficiency of the diesel engine.
Modern Modifications for Enhanced Efficiency
In more recent versions of the diesel engine, the pre-chamber and the combustion chamber are modified for maximum combustion and acoustical attenuation. The engine is turbocharged for maximum performance and power output. Digital controls have replaced the traditional analog types for more precision and controlled fuel injection rates and timings to enhance combustion and reduce exhaust gases. The noxious nitrous oxide (NOx) fumes are subjected to emission treatments like the Exhaust Gas Recirculation (EGR) and Selective Catalytic Reduction (SCR) to minimize emissions in various ways.
Engine Modifications for Enhanced Performance
Combustion Chamber Modifications
Newer diesel engines have combustion chambers sized and configured to achieve maximum combustion rates. The greater the combustion rate, the higher the power output and fuel efficiency and lower the exhaust emissions.
Sound Attenuation in Diesel Engines
Most people associate the diesel engine with high levels of noise. This noise occurs mainly when starting a diesel engine, as the fuel is injected into the pre-chamber and is forced to vaporize at a high temperature. Recent advancements in sound attenuation materials and strategies have enabled engineers to reduce noise levels to a significant extent. This is done by fitting the pre-chamber with sound attenuation pockets. These pockets are spaced and designed such that they nullify the detonation waves caused during combustion. Alternatively, these pockets are filled with porous or metallic ceramic pellets, which are coated with platinum or rhodium. Platinum and rhodium act as catalysts to achieve complete combustion and the pellets attenuate the noise levels. Other modifications involve placing attenuating materials such as porous ceramic or sintered metal near the mouth of the passage connecting the pre-chamber to the combustion chamber.
Advanced Fuel Systems and Fuel Treatments
Advanced Common-Rail Fuel Injection
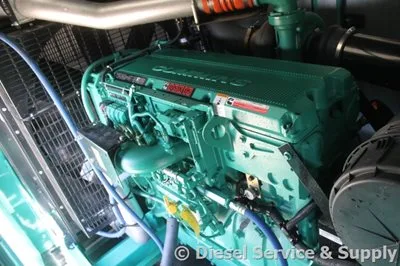
The Common-Rail Fuel (CRF) Injection system is a form of direct injection system, which injects fuel from a fuel tank into individual solenoid or piezoelectric valves. The fuel tank stores fuel at high pressures. This is an electronically monitored injection system, which allows for greater control over the fuel injection time and quantity. The CRF system is designed to maintain high pressure, which helps homogenize the fuel and air mixture by allowing for finer vaporization of fuel. This paves the way for more complete combustion, leading to greater power output and lower exhaust emissions. Recent advances in this system include modifications which allow for as many as five fuel injections per combustion cycle, thereby improving fuel economy. In fact, CRF systems are associated with a 20 percent decrease in fuel emissions and 5 percent improvement in fuel economy.
Fuel Composition and ULSD
Diesel fuel is typically high in sulfur content. Diesel produces high particulate matter emissions on combustion, which clog emission devices and hamper engine performance. However, with EPA (Environmental Protection Agency) mandates that went into effect in 2006, a newer version of diesel has been formulated with sulfur content as low as 15 parts per million (ppm). It is known as Ultra-Low-Sulfur Diesel or ULSD and has very low exhaust gas emissions.
Digital vs. Analog Controls
Analog Controls in Diesel Engines
Traditionally analog controls were integrated into diesel engines to monitor their function. Analog controls work well for a diesel engine that powers small appliances such as a power generator used for backing up a small facility like a small building.
Digital Controls in Diesel Engines
Digital controls are highly integrated and report the real-time status of all aspects – fuel, engine oil and coolant levels, engine temperatures, battery status, transfer switch status – of the diesel engine, accurately and simultaneously. This helps any technician monitoring the engine get an overview of the entire system on one screen and helps them locate and solve any problem quickly. In larger facilities, digital controls provide greater reliability, with built-in redundancy allowing for continual system function in case a component or a part of a circuit fails. Digital controls also increase the efficiency of an engine and reduce exhaust emissions since they automatically make the necessary adjustments to the fuel rate input and injection timing under varying load conditions.
Emission Treatments for Diesel Engines
Exhaust Gas Recirculation (EGR)
Diesel combustion occurs at very high temperatures and NOx is formed as a byproduct. NOx emissions at certain levels are harmful to the atmosphere and need to be regulated. EGR is one of the treatments which diesel engine manufacturers utilize to lower the NOx emission. In this treatment, part of the exhaust gases are re-circulated into the engine and mixed with the air in the combustion chamber. This process lowers the adiabatic flame temperature and increases the heat capacity of the mix, allowing for combustion at a much lower temperature and reducing NOx formation, which is maximized at high temperatures and in the presence of ample oxygen.
Selective Catalytic Reduction (SCR)
Selective Catalytic Reduction (SCR) utilizes a reducing catalyst such as anhydrous or aqueous ammonia, or urea to convert NOx into diatomic nitrogen and water. Although this method was patented in 1957 and has been in use for a long time for waste management systems and commercial boilers, its integration with diesel engine driven appliances, such as power generators, is a recent phenomenon. It is known to reduce NOx emissions in a range of 75–95%.
Conclusion: The Future of Diesel Engines
These are all just a few examples of some of the exciting new advancements that are being applied to diesel engines and diesel-powered generator sets. With market forces constantly pressuring for stricter engine and generator requirements, we should continue to see substantial improvements in engine modifications, fuel system efficiencies, expanded digital controls, emission treatments, and more over the coming years. All of which should help to make the tried and true diesel engine an even stronger power generation staple for many years to come.